Your Overview to Comprehensive Welding Inspection Milwaukee Solutions
Your Overview to Comprehensive Welding Inspection Milwaukee Solutions
Blog Article
How Welding Examination Adds To Long Life and Integrity in Construction Jobs
Welding evaluation offers as a foundational aspect in guaranteeing the durability and integrity of fabrication projects. By methodically identifying prospective flaws throughout numerous stages of production, welding examinations not only avoid costly failures however additionally cultivate a society of high quality guarantee within the group.

Relevance of Welding Assessment
Making certain quality through welding evaluation is a vital component of any kind of fabrication job. It functions as a guard to validate that welding procedures satisfy established standards and specifications, thereby enhancing the total honesty of the framework or part being made. Welding examination is not simply a procedural step; it is a crucial method that assists determine prospective issues early, making certain that they are attended to prior to they intensify right into significant problems.
The importance of welding inspection can be emphasized by its duty in maintaining safety and resilience. Welded joints are commonly based on extreme conditions, and any kind of flaws can endanger the efficiency and durability of the final item. By carrying out rigorous evaluation protocols, companies can guarantee compliance with industry laws, consequently reducing threats associated with structural failings.
Furthermore, effective welding evaluation fosters confidence among stakeholders, including customers and regulative bodies, that the project satisfies the finest quality standards. This not just improves the reputation of the maker yet also adds to long-term expense savings by staying clear of rework and potential responsibilities. Ultimately, welding assessment is important to the success and reliability of construction tasks, reinforcing the worth of quality guarantee in design practices.
Typical Welding Issues
Welding issues can considerably weaken the architectural honesty of produced components, making their identification and rectification crucial. Common welding problems can be generally categorized right into 3 types: geometric, metallurgical, and service-related.
Geometric defects consist of concerns such as undercutting, where the base metal is eroded at the side of the weld, and too much convexity, which can bring about stress focus factors. These problems can compromise the toughness and resilience of the weld joint.
Metallurgical defects arise from inappropriate welding treatments or materials, resulting in problems such as porosity, where gas pockets create within the weld, and lack of fusion, which happens when the weld metal fails to bond effectively with the base steel. These issues can substantially damage the weld's efficiency.
Service-related problems might not become noticeable till after the element remains in use. Instances include fracturing because of thermal stress or tiredness, which can result in catastrophic failures otherwise dealt with.
Understanding these common defects encourages makers to execute reliable evaluation approaches that enhance the dependability and longevity of their jobs, inevitably guaranteeing safety and security and performance requirements are fulfilled.
Inspection Methods and Methods
A detailed strategy to evaluation methods and approaches is important for minimizing and determining welding flaws in manufacture projects. Various approaches are utilized to make sure the honesty of welds, consisting of visual examination, ultrasonic testing (UT), radiographic testing (RT), magnetic bit screening (MT), and color penetrant screening (PT) Each technique has its staminas and certain applications.
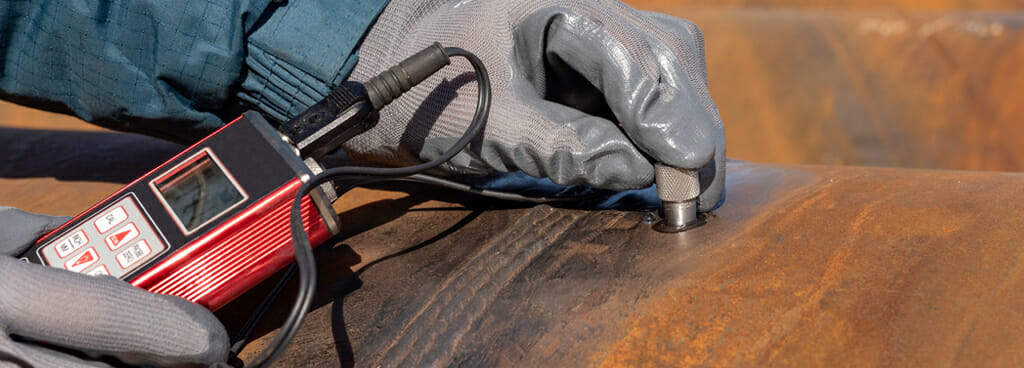
Magnetic particle screening is beneficial for detecting surface and near-surface issues in ferromagnetic products. By using a magnetic field and using ferrous particles, inspectors can recognize stoppages effectively. Finally, dye penetrant screening highlights surface-breaking defects with the application of a color that permeates into splits, making them visible under ultraviolet light.
Employing a combination of these methods makes certain a rigorous analysis, boosting the reliability of welded frameworks.
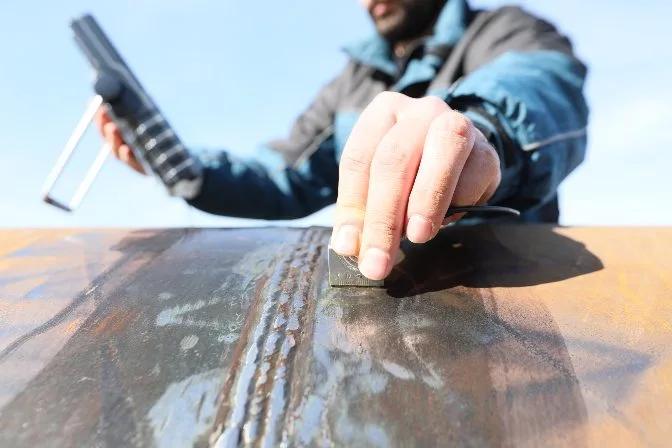
Impact on Task Long Life
Reliable examination methods dramatically affect the durability of fabrication tasks. By recognizing possible flaws and disparities in welding processes, assessments make certain that frameworks are built to withstand functional anxieties with time. When welds are extensively checked out, the probability of undiscovered issues, which might bring about architectural failures, is minimized.
Normal assessments assist in adherence to industry criteria and policies, which are crucial for ensuring the resilience of bonded joints. Such compliance not just improves the honesty of the task however additionally guarantees stakeholders regarding the high quality of the work. Furthermore, prompt detection of problems allows for restorative activities to be taken early, preventing pricey repairs or total overhauls down the line.
Furthermore, efficient inspection methods cultivate a culture of quality control within manufacture groups. They are a lot more most likely to stick to best methods and keep high standards throughout the production process when workers are mindful that their work will be rigorously examined. Inevitably, this dedication to quality not only prolongs the life expectancy of the task yet likewise reduces upkeep prices, therefore boosting the total financial feasibility of manufacture undertakings.
Enhancing Dependability in Manufacture
Dependability in manufacture is dramatically improved with extensive evaluation processes that attend to possible weaknesses in welding practices. Reliable welding examination not just identifies flaws early but also gives essential comments to welders, making sure adherence to established criteria and specs. By utilizing non-destructive screening methods, such as ultrasonic or radiographic examinations, producers can determine the integrity of welds without endangering the material.
In addition, routine assessments promote a culture of top quality and accountability amongst fabrication groups. When welders recognize that their work undergoes strict analyses, they are more probable to follow best methods and practices. This proactive technique minimizes the danger of pricey failures during the learn the facts here now functional phase of a job.
In addition, comprehensive paperwork of evaluation results develops an important database of details that can be used for future projects. Patterns in issues can be analyzed to enhance welding methods and training programs (Welding Inspection Milwaukee). Ultimately, boosting reliability in fabrication with detailed examination processes not just enhances the life-span of the made components however also strengthens stakeholder confidence in the task's general high quality and durability. Purchasing robust welding evaluation methods is necessary for attaining lasting integrity in any kind of construction undertaking.
Conclusion
In recap, welding assessment serves as an important element in making sure the longevity and integrity of manufacture jobs. By identifying problems early and employing non-destructive screening techniques, inspections cultivate a culture of high quality guarantee that abides by sector requirements. The systematic documents of results not only promotes pattern evaluation but additionally improves accountability and architectural integrity. Inevitably, efficient welding evaluation techniques reinforce stakeholder self-confidence and considerably add to the economic viability of construction undertakings.
Welding examination offers as a foundational aspect in making certain the longevity and integrity of manufacture projects.Guaranteeing high quality through welding inspection is an important part of any fabrication job. Eventually, welding inspection is integral to the success and reliability of construction jobs, strengthening the worth of top quality guarantee in design techniques.
A her explanation thorough approach to examination techniques and methods is necessary for identifying and mitigating welding flaws in construction jobs.In summary, welding examination serves as a vital element in making sure the longevity and dependability of manufacture tasks.
Report this page